3D printing has ushered in a new era of innovation, transforming industries from healthcare to aerospace. In mechanical engineering, this groundbreaking technology is revolutionizing how designs are created, tested, and brought to life. This guide will take you through the essentials of 3D printing in mechanical engineering, covering its applications, benefits, and the technical details that make it such a game-changer.
What is 3D Printing in Mechanical Engineering?
3D printing, also known as additive manufacturing, is a process of creating three-dimensional objects layer by layer from a digital design. In mechanical engineering, 3D printing allows for the creation of complex geometries, prototyping, tooling, and even end-use parts with unmatched precision.
The core principle is simple: instead of subtracting material (as in traditional machining), the material is added where needed, resulting in minimal waste and enhanced efficiency. This innovative technique aligns perfectly with the needs of mechanical engineers who prioritize precision, efficiency, and adaptability.
The History and Evolution of 3D Printing
Though 3D printing may seem like a recent marvel, its roots trace back to the 1980s. Charles Hull, the inventor of stereolithography (SLA), laid the foundation for modern 3D printing. Since then, the technology has evolved, with newer methods like selective laser sintering (SLS), fused deposition modeling (FDM), and direct metal laser sintering (DMLS).
The past two decades have witnessed a surge in 3D printing applications within mechanical engineering. As the technology matured, engineers began leveraging its potential to streamline production cycles, test designs, and create prototypes rapidly.
Advantages of 3D Printing in Mechanical Engineering
The impact of 3D printing on mechanical engineering is vast and undeniable. Here are some of its key advantages:
- Cost Efficiency: Traditional manufacturing processes often involve high setup costs. 3D printing eliminates the need for molds, reducing expenses significantly.
- Design Freedom: Engineers can design intricate and complex parts that are impossible or too costly to produce with traditional methods.
- Rapid Prototyping: Creating prototypes quickly enables engineers to test, refine, and iterate designs at a fraction of the time compared to traditional methods.
- Material Efficiency: Additive manufacturing minimizes material wastage by only using the amount required for the design.
- Customization: 3D printing allows for tailor-made solutions, particularly beneficial in mechanical engineering applications like custom tooling or niche part production.
3D Printing Technologies Used in Mechanical Engineering
Fused Deposition Modeling (FDM)
FDM is one of the most accessible and widely used 3D printing technologies. It involves melting and extruding thermoplastic material layer by layer. Its affordability makes it a popular choice for prototyping in mechanical engineering.
Stereolithography (SLA)
SLA uses a laser to cure liquid resin into solid layers. Known for its precision, SLA is ideal for creating detailed mechanical components and intricate prototypes.
Selective Laser Sintering (SLS)
This method uses a laser to sinter powdered material into solid layers. SLS is often used to produce durable, functional parts that can withstand mechanical stress.
Direct Metal Laser Sintering (DMLS)
A go-to choice for creating metal parts, DMLS is a highly advanced technology in mechanical engineering. It offers incredible strength and precision, perfect for aerospace or automotive components.
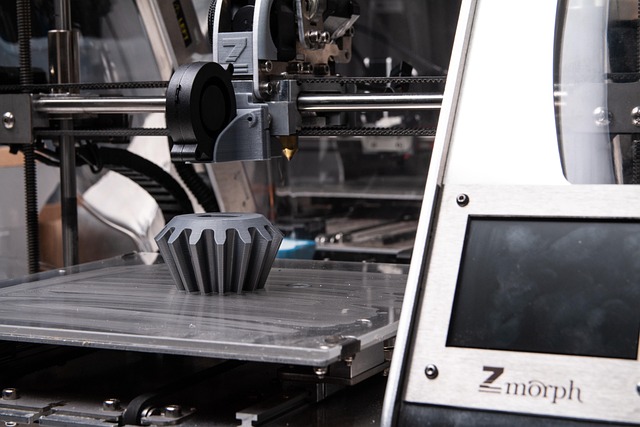
Materials Used in 3D Printing for Mechanical Engineering
The versatility of 3D printing materials ensures its applicability across a broad spectrum of mechanical engineering projects.
- Plastics: ABS, PLA, and nylon are popular choices for prototyping and lightweight components.
- Metals: Titanium, stainless steel, and aluminum are commonly used for creating robust mechanical parts.
- Composites: Carbon fiber-reinforced materials provide strength while maintaining a lightweight structure.
- Resins: Used for high-detail prototypes, resins offer smooth finishes and exceptional precision.
Applications of 3D Printing in Mechanical Engineering
Prototyping and Product Development
Prototyping has always been a cornerstone of mechanical engineering. With 3D printing, engineers can create functional prototypes rapidly, allowing for extensive testing and iteration before finalizing a design.
Tooling and Jigs
Traditional tooling methods are expensive and time-consuming. 3D printing offers a cost-effective solution for creating custom tools, jigs, and fixtures tailored to specific projects.
Lightweight Structures
Additive manufacturing enables engineers to create lightweight, high-strength structures. This application is particularly valuable in industries like aerospace and automotive.
Customized Solutions
From medical implants to bespoke machinery components, 3D printing facilitates custom designs that address unique mechanical challenges.
Spare Parts Production
Instead of maintaining extensive inventories, mechanical engineers can use 3D printing to produce spare parts on demand, reducing storage costs and downtime.
The Process of 3D Printing in Mechanical Engineering
Step 1: Creating the Digital Model
The process begins with designing a 3D model using CAD (Computer-Aided Design) software. Tools like SolidWorks and AutoCAD are staples for mechanical engineers.
Step 2: Preparing for Printing
Once the design is finalized, slicing software divides the model into layers and generates a file readable by the 3D printer.
Step 3: Printing the Part
The 3D printer follows the instructions in the sliced file, depositing material layer by layer to create the physical object.
Step 4: Post-Processing
Depending on the technology used, post-processing may include removing supports, sanding, or curing the part to achieve the desired finish.
Challenges and Limitations of 3D Printing in Mechanical Engineering
While the benefits are numerous, 3D printing does come with its challenges:
- Material Limitations: Not all materials are compatible with 3D printing.
- Surface Finish: Depending on the technology, printed parts may require additional finishing.
- Size Constraints: Most printers have size limitations, which can be restrictive for large-scale mechanical projects.
- Initial Costs: High-end 3D printers and materials can be expensive, though they often pay off in the long run.
Future of 3D Printing in Mechanical Engineering
The future of 3D printing in mechanical engineering is undeniably bright. Advancements in materials, technology, and techniques are paving the way for more efficient and innovative applications. Concepts like 4D printing, where objects can change shape or function over time, are on the horizon.
Additionally, the integration of AI and machine learning into 3D printing promises to optimize design and production processes further, enhancing the capabilities of mechanical engineers worldwide.
FAQs
What is 3D printing in mechanical engineering?
3D printing, or additive manufacturing, in mechanical engineering involves creating parts and prototypes layer by layer from digital designs, offering precision and efficiency.
What materials are commonly used in 3D printing for mechanical engineering?
Common materials include plastics like ABS and PLA, metals like titanium and aluminum, composites, and resins.
How is 3D printing different from traditional manufacturing?
Unlike traditional methods that subtract material, 3D printing adds material layer by layer, reducing waste and allowing for intricate designs.
What are the challenges of using 3D printing in mechanical engineering?
Challenges include material limitations, size constraints, surface finish requirements, and high initial costs.
Can 3D printing replace traditional manufacturing?
While 3D printing offers numerous advantages, it is often used alongside traditional methods rather than replacing them entirely.
What are some industries benefiting from 3D printing in mechanical engineering?
Industries like aerospace, automotive, healthcare, and consumer goods benefit greatly from 3D printing applications in mechanical engineering.
Conclusion
3D printing in mechanical engineering is more than just a tool—it’s a transformative force reshaping how engineers approach design, prototyping, and manufacturing. Its ability to create intricate, cost-effective, and efficient solutions has opened doors to endless possibilities. As the technology continues to evolve, mechanical engineers who embrace 3D printing will be at the forefront of innovation, driving progress across industries.